I am hoping to get some feedback here, so please register if you haven’t already and comments will be appreciated.
Snecked Blades
In the course of my research I have found that the only planes that were made with snecked irons were shoulder planes, and the occasional thumb and chariot planes – these were side snecked as in my 11-s smoothing plane here (double sided sneck).
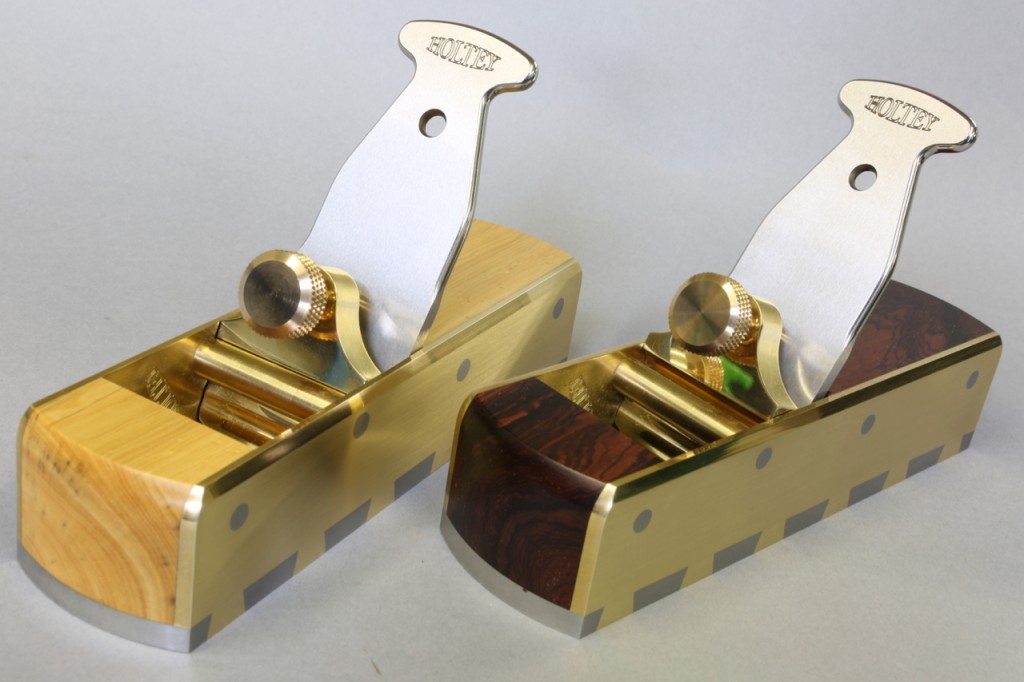
Mitre planes usually have top snecked irons, as in my No 10 shown here.
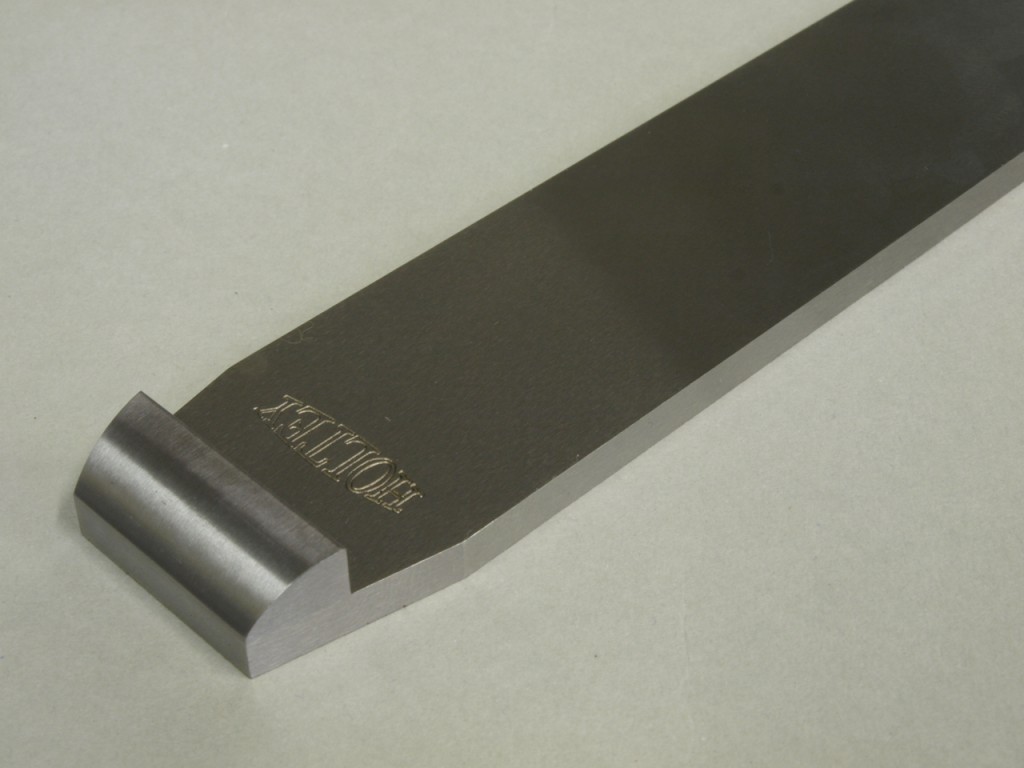
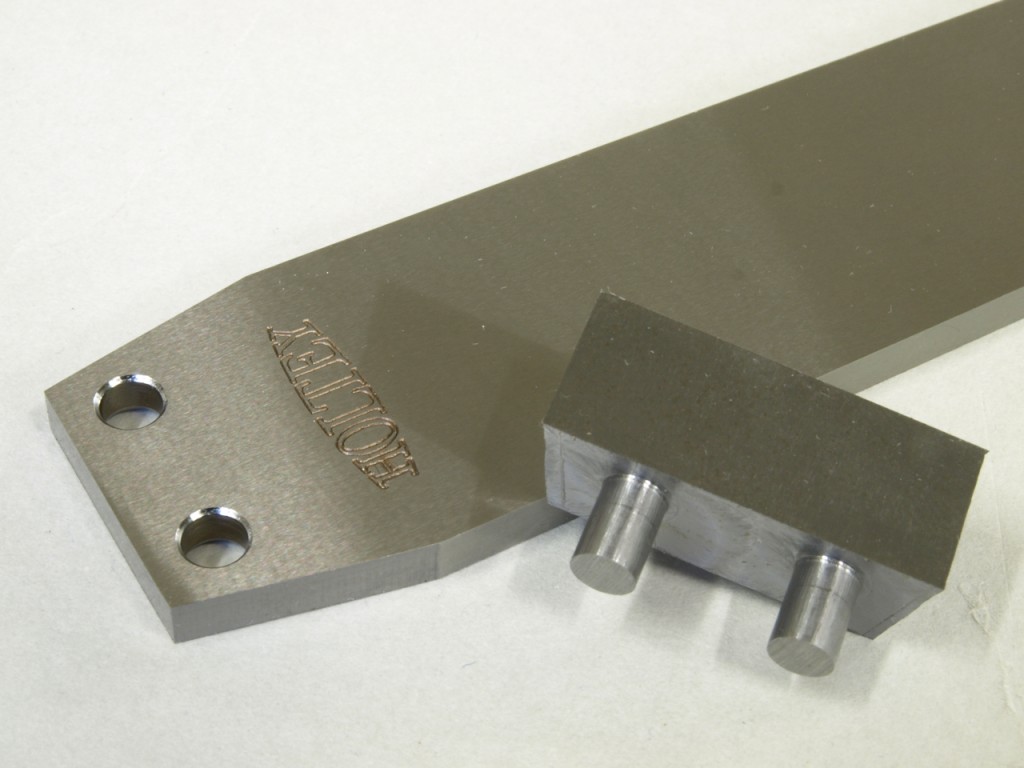
I can’t understand why smoothers and panel planes etc did not have snecked irons. Of course top snecking would require a longer blade as lever cap or wedge would restrict their use. A side sneck should still work on these planes.
Is it possible that the use of chip breakers had something to do with this?
I am working on a development plane at the moment and planning to make it a non-adjuster plane. I feel that having a snecked iron will make a considerable difference in setting up the blade. I am also wondering if users choose to use a non-adjuster plane because it is better or is it an elitist thing?