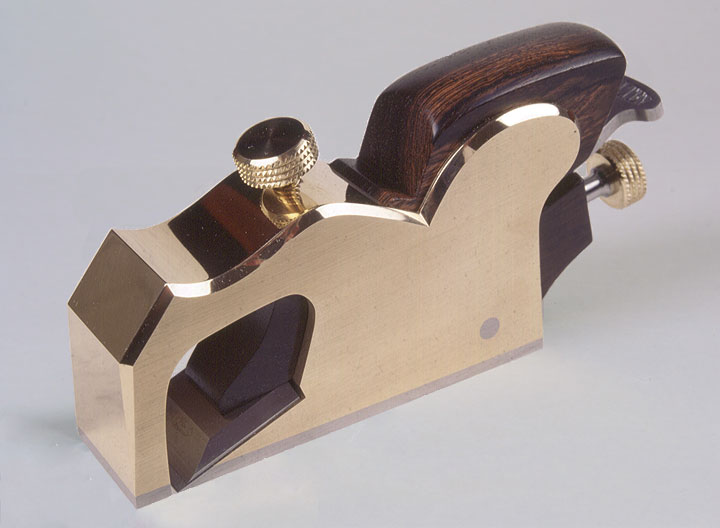
This is one of only six A27 Bullnose planes I made many years ago. This was made by casting as were the original Norris. There were one or two downsides to this method of production so for some time I have been contemplating making a fabricated version using traditional dovetails. Now that time has arrived. It will be a limited edition, and as you will have realised I am moving away from traditional infill planes so unlikely that I will make these again. This is the second plane in the set of three low angle planes I have been making for some of my customers – A27, A28 and A31.
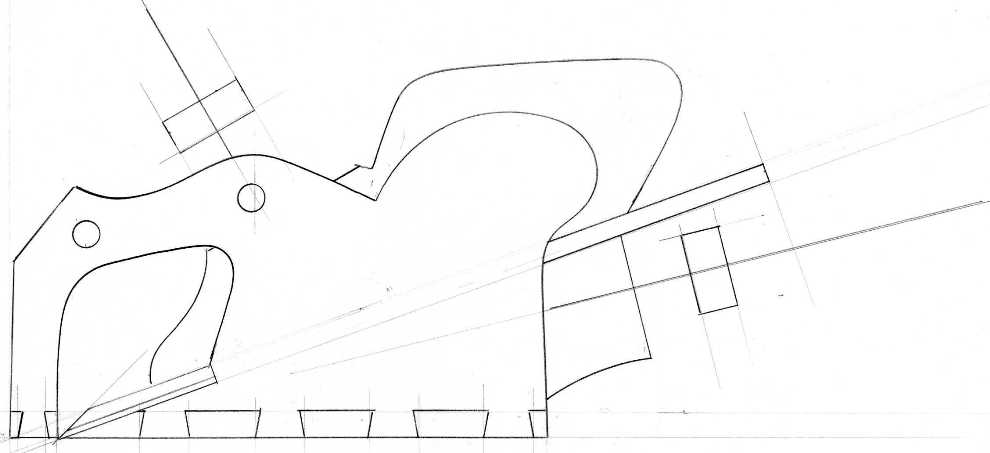
A quick line drawing of the proposed plane. This is being made with naval brass sides (CZ112) and malleable cast iron for the bottoms, fore-end and bridge sections. I will be using a traditional wooden wedge and the adjuster housing is also rosewood. To my knowledge a Bullnose plane has not been made since Norris’s time in the 1920s – when it cost 23/- (shillings). I shall have to charge a little more. I have also moved the goalposts in regards to quality and precision.
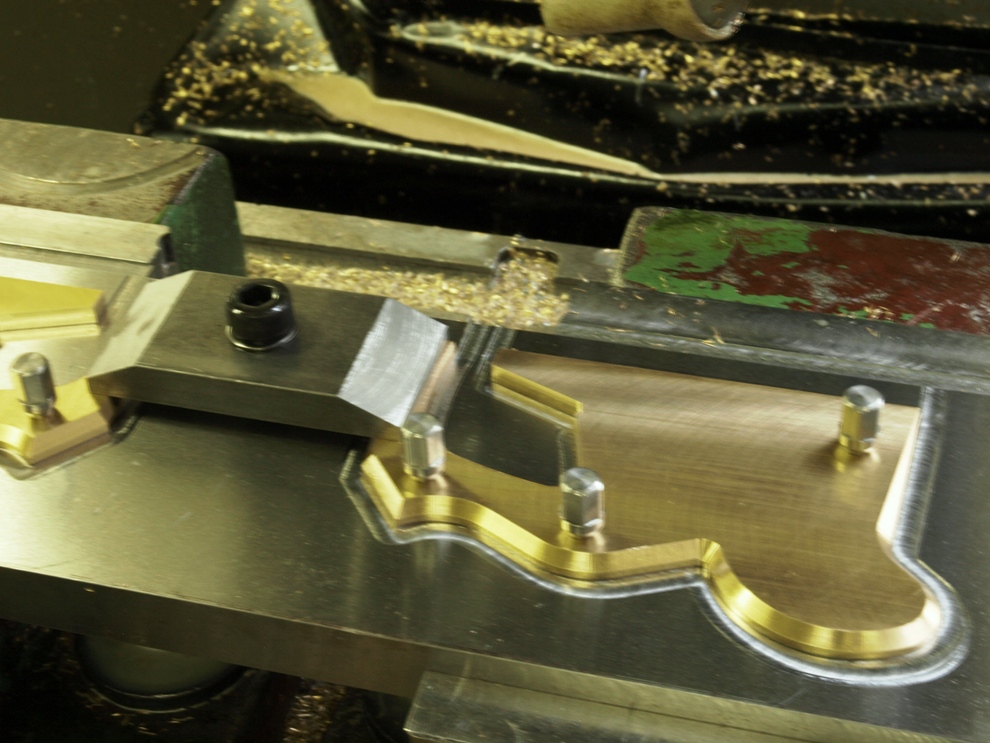
The sides being routed on the CNC mill. All the precision work holding tools and jigs I made myself before starting this. Every plane I make has individual jigs and work holding which are surface ground to a high precision. My tool room has been built up over many years and is, I believe, the only one of its kind. You will not find this standard of precision anywhere else.

The riveting holes, include a 60 degree chamfer, which provides the jig fixing and positive location.
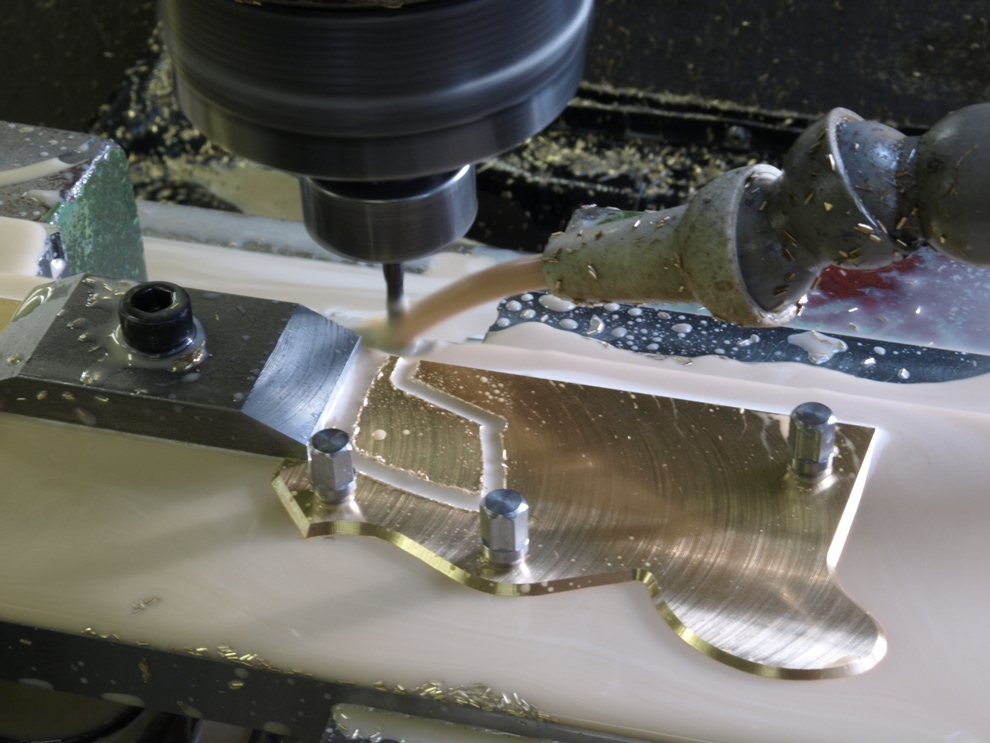
The mouth being cut out last as a separate job as it needs an additional clamping to support the front end – which can be seen to the left hand side of the picture.
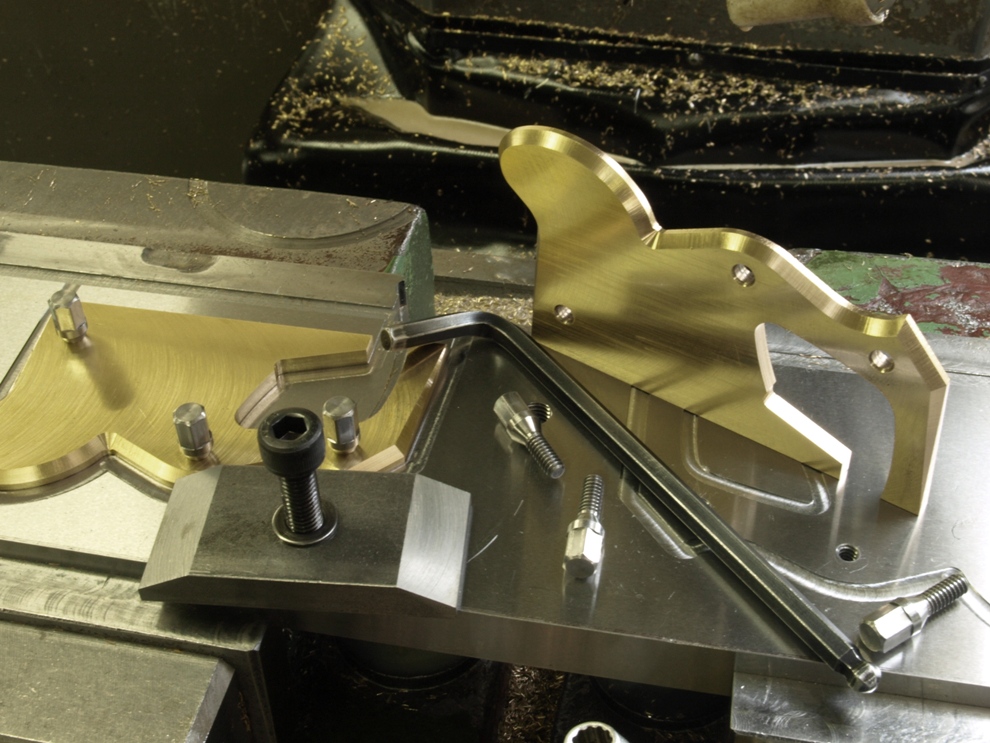
Here is the finished side except for the dovetailing. It includes its mirror partner completing the pair.
As usual to be continued when I next have an opportunity.